Today, warehouses are vital to logistics, influencing the effectiveness and output of the supply chain. There are two main ways to organize the coming of freight to warehouses: First Come, First Serve (FCFS), or according to a schedule. Each of these choices has a unique impact on logistics, like driver waiting times and the reliability of deliveries.
FCFS allows for flexibility because the trucks can be processed in the order they arrive, but that can make for unpredictable waiting times. Scheduled operations allow for more structure by assigning specific time slots and thus minimize congestion, enabling more predictable planning. Which system is selected is based upon the operation’s specific needs and requirements of the customer.
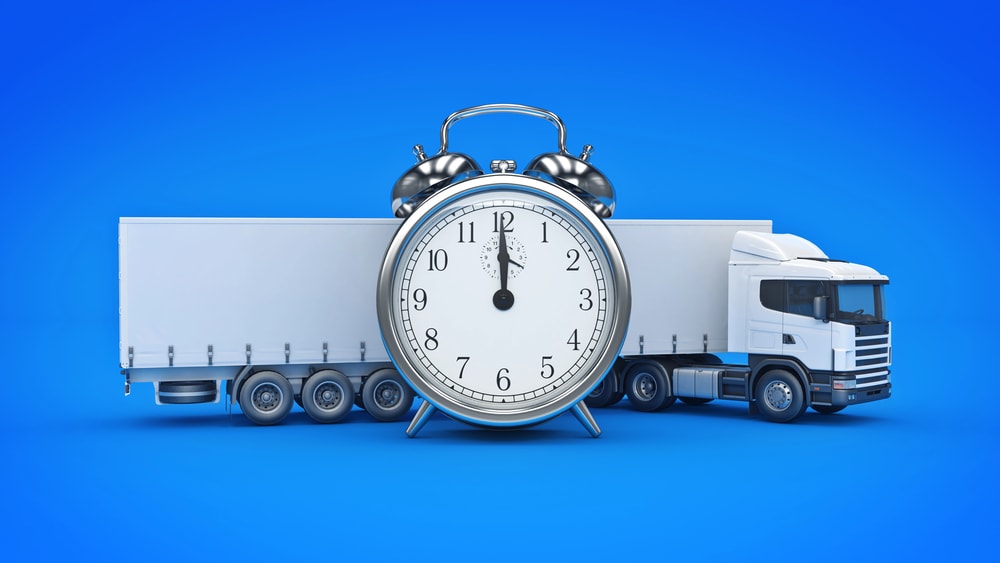
What FCFS Truly Means in Freight Shipping
In freight shipment, FCFS is a method of prioritizing trucks for loading and/or unloading, based on the time each arrives at a given facility. In other words, the first truck to arrive is the first truck to get serviced, with the later-arriving ones having to wait their turn. Most facilities in the country use this system as it is very straightforward.
With an FCFS model, drivers need to plan their schedules based on their place in the queue, which affects how quickly they can finish a delivery or pickup. There is considerable variation in how this approach is taken per facility because some locations can handle a high volume of trucks much more efficiently than others. Drivers need to understand FCFS because it plays a big role in how much time they spend on the road and their ability to make the most out of their time.
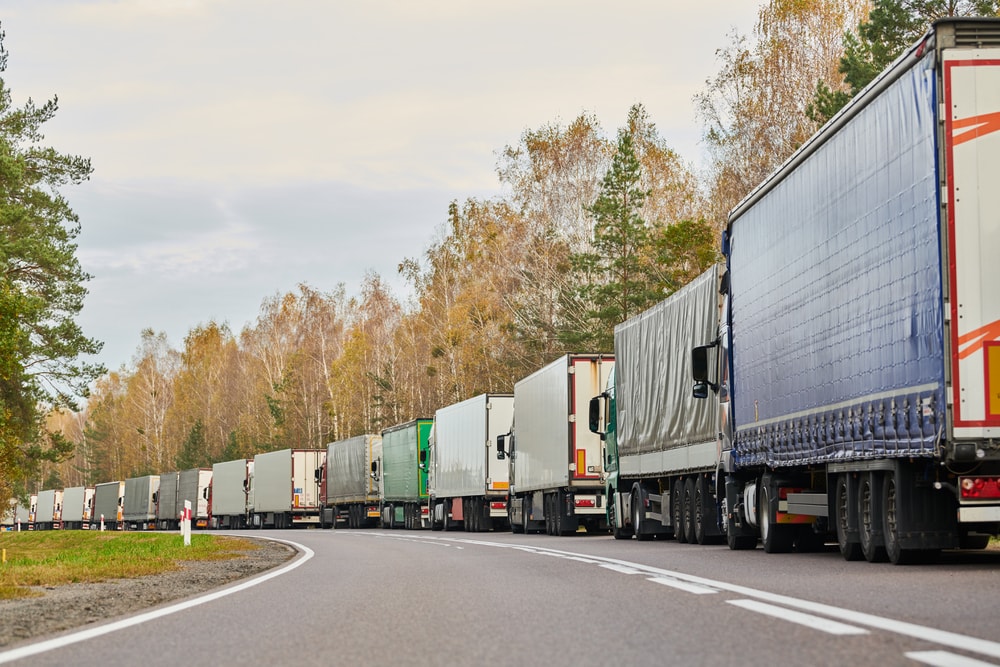
How Scheduled Operations Work in Warehouse Logistics
Scheduled operations in warehouse logistics involve the use of a structured scheduling system that assigns specific appointment times for trucks to arrive for loading or unloading. The system uses advanced scheduling algorithms to ensure freight flows efficiently by carefully planning each truck’s appointment time. Operating under scheduled times is less flexible than FCFS and requires strict adherence to these time slots for maintaining the smooth function of the warehouse.
Precise appointment times cannot be overstated in scheduled operations. Pre-assigned times for each truck prevent congestion at the facility and avoid bottlenecks that would normally come from too many trucks arriving at any one time. Predictability benefits appointment-based facilities in managing resources and smoothing out the process for quicker turnarounds, ensuring better efficiency in the overall chain of logistics.
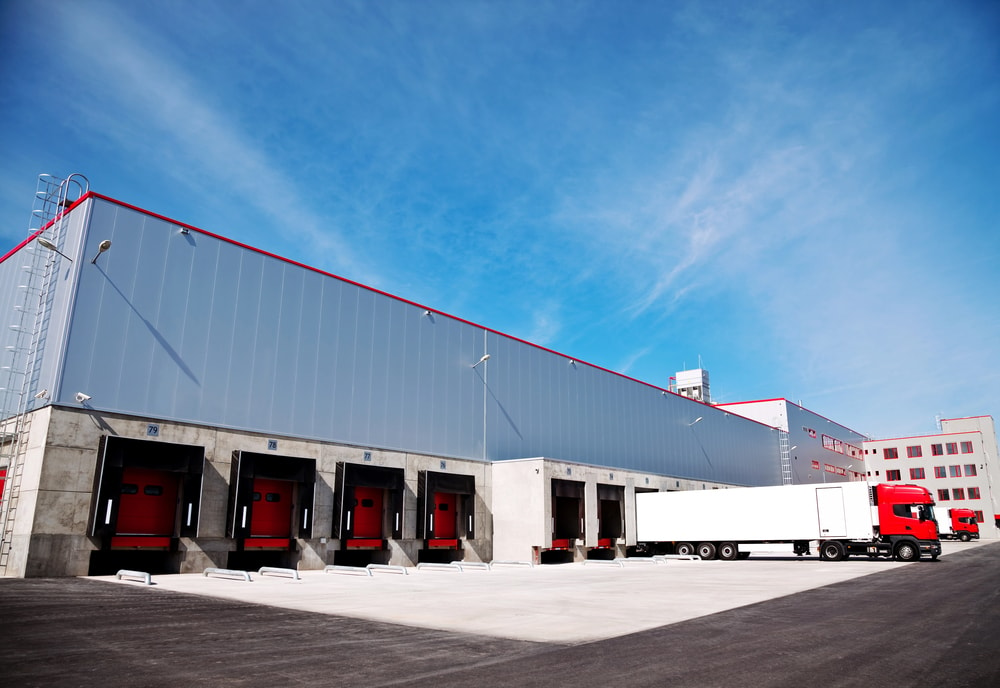
Advantages of FCFS in Freight Shipping
First come first serve in freight shipping provides flexibility for carriers who do not have tight schedules. FCFS’s scheduling algorithm allows carriers to appear at a destination, load, or offload freight at their convenience without a pre-set appointment. In this way, it can help accommodate unpredictable road conditions or delays. This is an option that gives drivers the leeway to prioritize the routes based on other factors rather than an exact window for delivery.
Ample yard dock space is one of the advantages of FCFS facilities that accommodate multiple trucks arriving at the same time to ensure loading and offloading are effectively executed even when at peak hours. Providing smooth workflow with more flexibility, FCFS facilities can reduce congestion and help drivers get in and out without having to stay in a queue for hours.
Downsides of FCFS Operations
FCFS operations can lead to inefficiencies, particularly when it comes to long wait times for truck drivers. Most of the time, drivers spend their time in a queue, often up to hours, waiting for a turn to load or unload merchandise. The variability here might break schedules and raise shipment costs because the carrier has to budget for this extended downtime. This is particularly notable for truck drivers, who lose time in congested parking lots.
Congestion of this nature affects their hours of service and reduces overall productivity. Because there lacks a structured schedule, several trucks more often than not arrive at the same time, creating a backlog of semi-trucks parked around the facility. This is a problem that further prolongs loading and unloading and adds inefficiencies. It can also impact the drivers who have to face increased levels of stress and the possibility of shipping delays which may influence customer satisfaction and logistics performance.
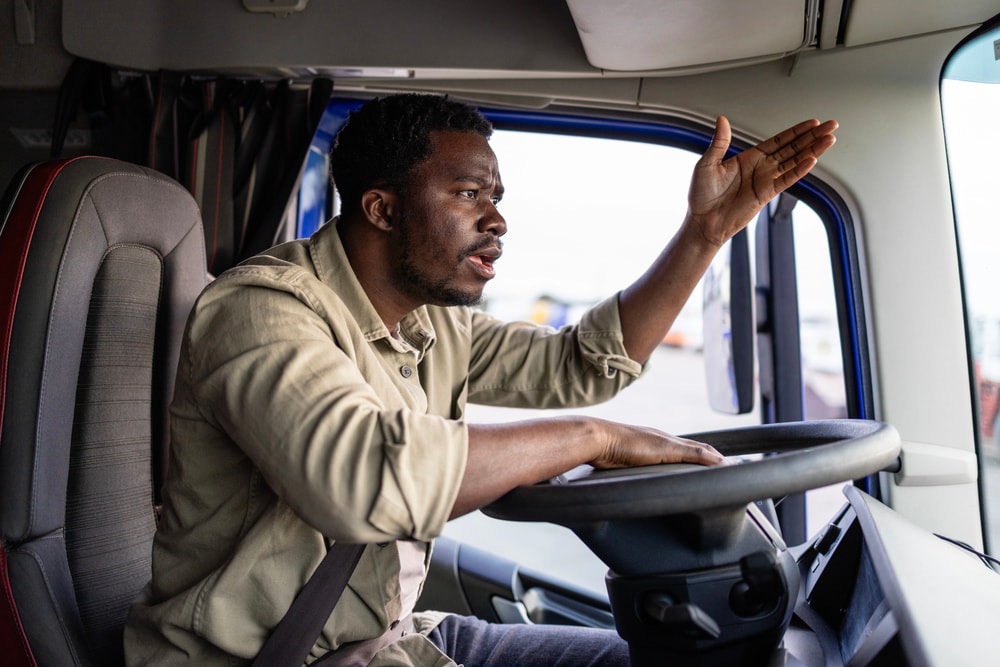
Benefits of Scheduled Warehouse Operations
Scheduled warehouse operations offer a structured approach that reduces wait times for drivers and trucks. By assigning specific time slots, warehouse managers can ensure the smooth flow of goods in and out of the facility. This method not only reduces idle time for trucks but also optimizes the availability of resources like crane operators and forklift drivers. When workers know exactly when shipments are arriving, they can plan their shifts more effectively, leading to a more productive and streamlined environment.
In addition to reducing downtime, scheduled systems enhance the overall efficiency of warehouse operations. By efficiently loading and unloading trucks according to a pre-arranged schedule, receivers can maximize their workforce and avoid the bottlenecks often experienced in an FCFS timeframe. This scheduling method allows warehouses to manage their resources more effectively, ensuring shipments move through the facility without unnecessary disruptions.
Scheduled warehouse operations offer several advantages, especially in terms of efficiency and organization. By allowing for specific time slots for truck arrivals and departures, warehouse managers can reduce wait times for drivers and trucks. This helps to minimize truck queues and ensure that resources like crane operators and forklift drivers are fully utilized. With better shift planning, workers can operate better, leading to a more productive and organized warehouse environment.
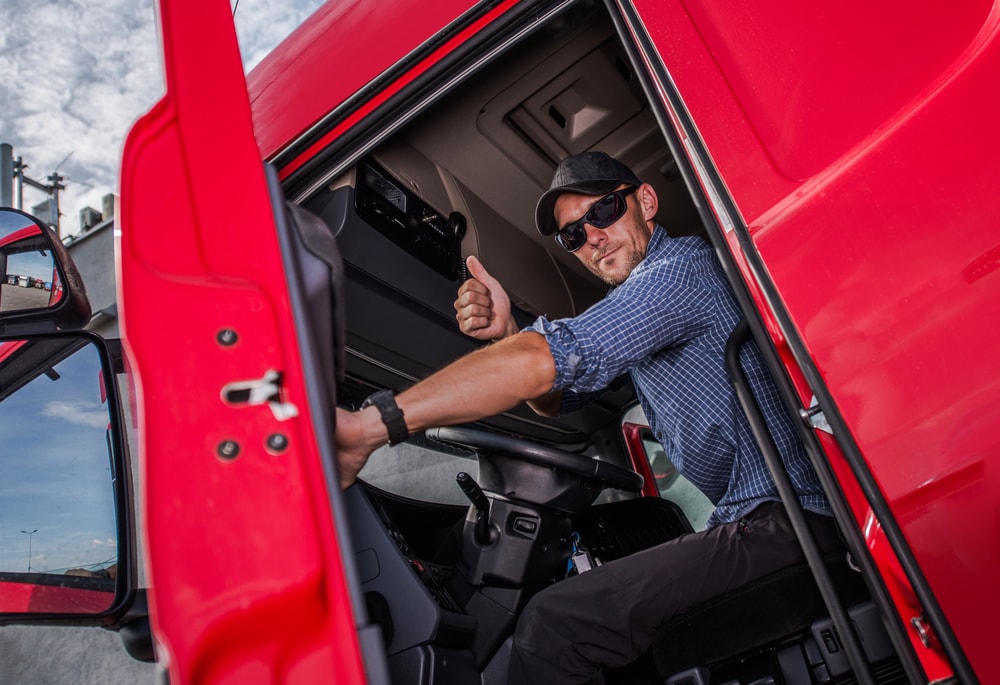
Comparing FCFS and Scheduled Operations
When comparing FCFS and scheduled operations, both have distinct advantages depending on the nature of the freight being shipped and the structure of the industry. The FCFS operation provides flexibility to truck drivers by allowing them to appear without a pre-set time, which could be advantageous for shippers and receivers that have ample staffing and resources. This model would typically apply to those situations where concerns about time-sensitive goods are fewer, such as dry van shipments. In these cases, though, the lack of a set schedule can sometimes actually mean longer waiting times when the facilities are very busy.
On the other hand, scheduled operations provide a more structured approach, particularly important for time-sensitive goods like refrigerated freight. Those shippers and receivers using skilled labor, such as crane operators or forklift drivers, could better plan their schedules to minimize any wait time. This may further help to ease the processing of operations and decrease the uncertainty in delays for drivers and warehouse employees. But the trade-off here is that this efficiency does indeed come at the cost of less flexibility for the drivers who may get very rigid appointment times, reducing their time to attain other loads.
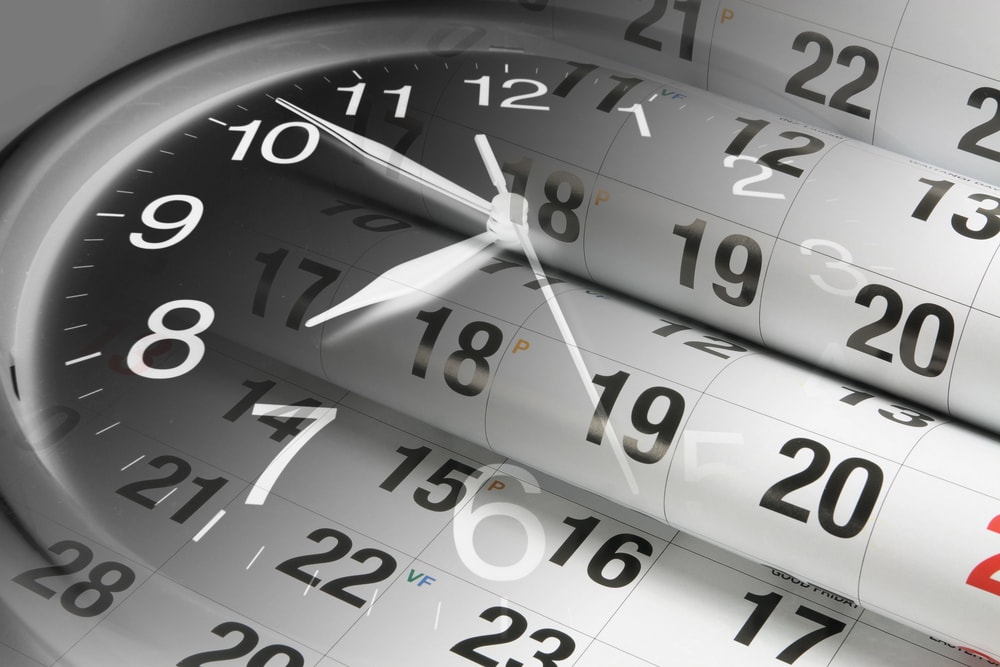
The Impact of Warehouse Operations on Shipping Prices
In the freight shipping industry, the choice between FCFS and scheduled operations can influence shipping costs. This causes delays, increased fuel consumption, and higher labor costs by the drivers, adding up to what you have to pay. On the contrary, scheduled warehouse operations make the entire process smoother by allocating a specific time slot for pickups and deliveries, reducing idle time and increasing overall efficiency.
Operating systems play a large role in determining the cost-effectiveness of each method. Advanced scheduling systems can manage resources, such as crane operators and forklift drivers, which will result in fewer delays and lower operational costs. This is an improvement compared to FCFS systems, which are at the mercy of several variables, including traffic and truck availability. The advantage of scheduled operations to companies is the ability to avoid many of the hidden costs associated with FCFS unpredictability. In turn, this can improve efficiency and enhance pricing.
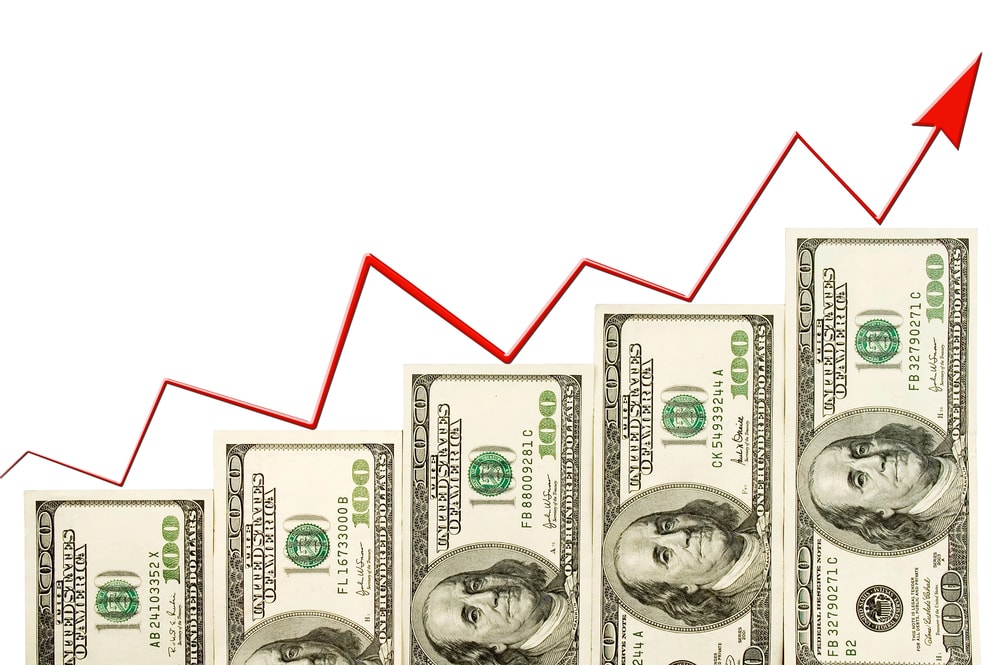
Choosing the Right Warehouse Operation Method for Your Needs
When selecting the right warehouse operation method for your logistics needs, understanding the benefits of both FCFS and scheduled operations is essential. FCFS will work best for shippers and receivers that employ skilled workers who know how to handle different types of loads in the shortest time to avoid any delay. This works when there is a need for flexibility because the trucks are being processed upon arrival, which caters to a logistics setup where arrival times may vary.
On the other hand, scheduled operations offer predictability and structure, making it easier to plan resource allocation. Shippers and receivers utilizing trained workers in scheduled operations enjoy smooth workflows, minimized wait time, and better utilization of equipment and personnel. The use of skilled workers trained in both the FCFS method and scheduled methods ensures that your clients easily toggle one way or another in maintaining efficiency regardless of the nature of the logistical challenges they face.
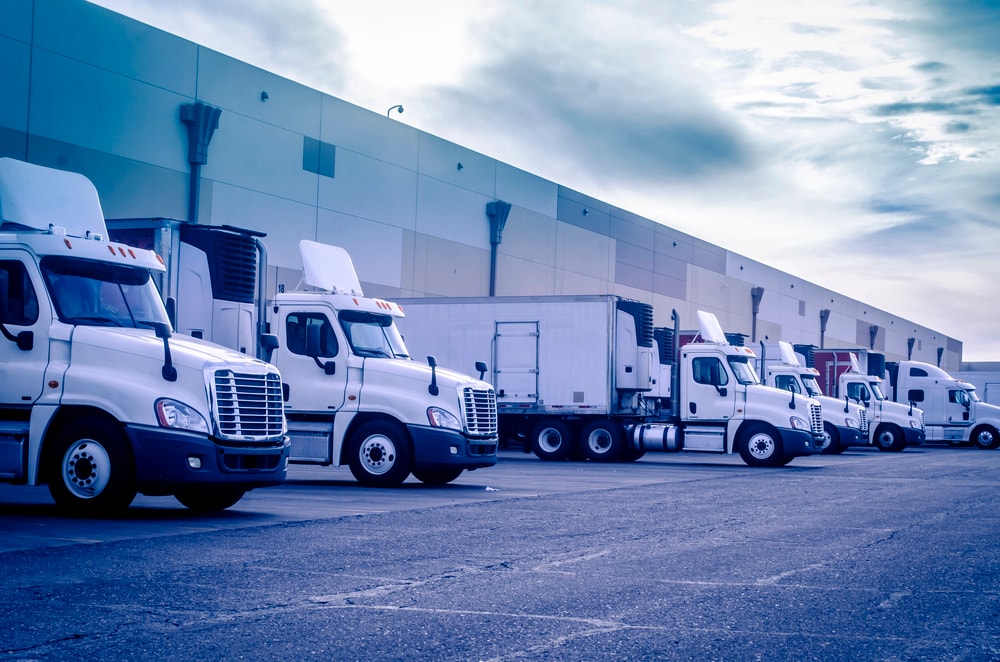
Conclusion
Both FCFS and scheduled operations offer different advantages, depending on what logistics your business requires. FCFS fills in the gaps by allowing trucks to be processed at any given time and is helpful if the timing is not entirely predictable. However, it does come with the potential trade-offs of wait times and congestion. Scheduled operations, on the other hand, are more organized, allowing for resources to be properly allocated and wait time reduced, but this requires strict adherence to set time slots. They satisfy different operational demands, and it really depends on the type of freight and the nature of your supply chain as to which method is most appropriate.
Understanding the differences between FCFS and scheduled operations allows for the optimization of your overall logistics strategy. In employing skilled workers to handle the workload under both systems, shippers and receivers alike will experience a smooth flow and cost reduction in operations. Whether flexibility or predictability is your priority, aligning your approach to warehouse operations with the specific needs of your business can lead to better resource management and more cost-effective logistics processes.